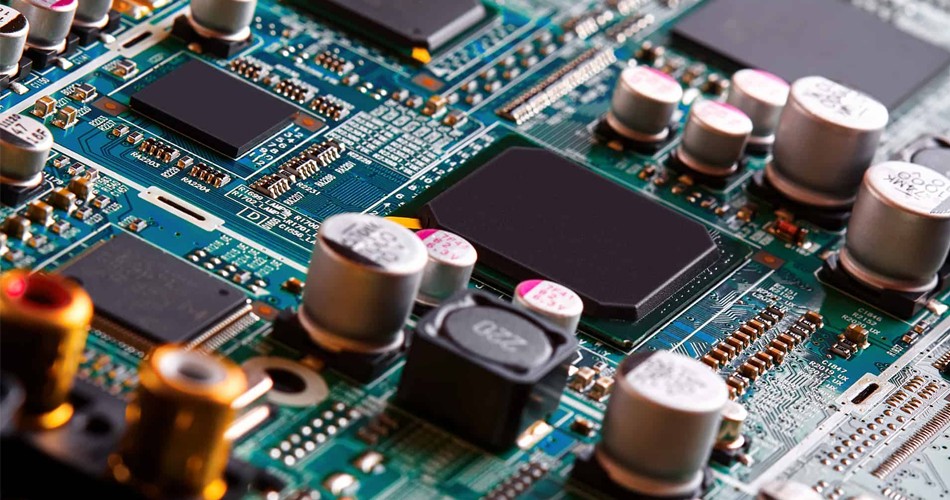
How to reduce the surface tension and viscosity in PCBA welding?
Whether reflow welding, wave soldering or manual soldering, surface tension is a negative factor for forming good solder joints. However, the surface tension can be used in SMT chip processing reflow -- when the solder paste reaches the melting temperature, it is on the balanced surface.
1、 Measures to change surface tension and viscosity
Viscosity and surface tension are important properties of solder. Good solder should have low viscosity and surface tension when melting. Surface tension is the nature of matter, whICh cannot be eliminated, but can be changed.
The main measures to reduce surface tension and viscosity in PCBA welding are as follows:
① Raise the temperature. Increasing the temperature can increase the distance between molecules in molten solder and reduce the attraction of molecules in liquid solder to surface molecules. Therefore, temperature rise can reduce viscosity and surface tension.
② Adjust the proportion of metal alloy. The surface tension of Sn is very large. Adding Pb can reduce the surface tension. It can be seen from the figure that when the lead content in Sn Pb solder is increased to 37%, the surface tension is significantly reduced.
③ Increase the active agent. This can effectively reduce the surface tension of solder, and can also remove the surface oxide layer of solder.
Using nitrogen to protect PCBA welding or vacuum welding can reduce high temperature oxidation and improve wettability.
2、 The role of surface tension in welding
The direction of surface tension is opposite to that of wetting force, so surface tension is one of the factors unfavorable to wetting.
Whether reflow welding, wave soldering or manual welding, surface tension is a negative factor for forming good solder joints. However, surface tension can be utilized in SMT chip processing and reflow welding.
When the solder paste reaches the melting temperature, under the effect of the balanced surface tension, it will produce the self alignment effect, that is, when the placement position of the components deviates slightly, the components can be automatically pulLED back to the approximate target position under the effect of the surface tension.
Therefore, the surface tension makes the requirements of reflow process on the mounting accuracy more relaxed, and it is easier to achieve high automation and high speed.
At the same time, because of the characteristics of "reflow" and "self positioning effect", SMT reflow soldering process has stricter requirements on pad design, component standardization, etc.
If the surface tension is not balanced, even if the mounting position is very accurate, there will be welding defects such as component position offset, monument, bridging, etc. after welding.
During wave soldering, due to the size and height of the SMC/SMD element body itself, or because the high element blocks the low element, the tin wave current coming from the front is blocked, and the shadow effect is caused by the influence of the surface tension of the tin wave current, which forms a current blocking area on the back of the element body that cannot be infiltrated by liquid solder, causing solder leakage.
Shenzhen PCB manufacturer and pcb designer explained how to reduce the surface tension and viscosity in PCBA welding.