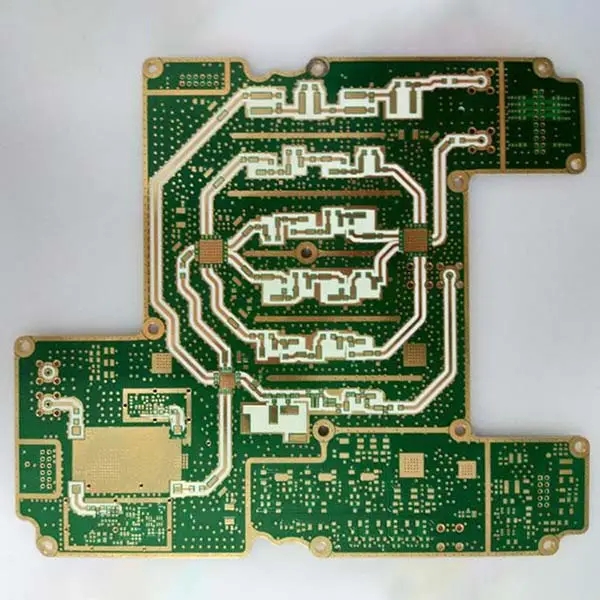
Circuit board engineer: ceramic circuit board processing technology
PCB manufacturing, PCB design, PCBA processing manufacturer will explain PCB engineer: ceramic PCB processing technology
There are many types of manufacturing technologies for ceramic products in circuit board factories. It is said that there are more than 30 kinds of manufacturing methods, such as dry pressing, grouting, extrusion, injection, tape casting and isostatic pressing. Because the electronic ceramic substrate is "flat" (square or circular), the shape is not complex, and the manufacturing process of dry molding and processing is simple and the cost is low, most of them use dry molding. The manufacturing process of dry pressed flat electronic ceramics mainly includes three aspects: blank forming, blank sintering and finishing, and circuit formation on the substrate.
1. Manufacturing of green blanks (forming)
Use high-purity aluminum oxide (Al2O3 with content ≥ 95%) powder (different particle sizes are required depending on the use and manufacturing method, such as from a few illiterates to tens of microns) and additives (mainly adhesives, dispersants, etc.) to form "slurry" or processing materials.
(1) Green blanks (or "green blanks") are made by dry pressing.
The dry pressing blank is made of high-purity aluminum oxide (the content of aluminum oxide used for electronic ceramics is more than 92%, and most of them are 99%) powder (the maximum particle size used for dry pressing shall not exceed 60 μ m. The particle size of powder used for extrusion, tape casting and injection shall be controlled within 1 μ M) add appropriate plasticizer and adhesive, mix evenly and then dry press the blank. At present, the generation of its square or round piece can reach 0.50mm, or even ≤ 0.3 mm (related to the size of the plate).
The blank after dry pressing can be processed before sintering, such as outline dimensions and drilling, but attention should be paid to the compensation of size shrinkage caused by sintering (enlarging the shrinkage size).
(2) The green billets are produced by tape casting.
Manufacturing+tape casting (uniformly coating the glue on the metal or heat-resistant polyester belt on the tape casting machine)+drying+trimming (processing such as holes can also be carried out)+degreasing+sintering and other processes of flowing glue (aluminum oxide powder+solvent+dispersant+binder+plasticizer, etc.). Automatic and large-scale production is available.
2. Sintering of green blanks and finishing after sintering. The green parts of ceramic substrates often need to be "sintered" and finished after sintering.
(1) Sintering of green blanks.
"Sintering" of ceramic green billets refers to the process in which the cavities, air, impurities and organic matters in the green billets (volume), such as dry pressing, are removed by volatilizing, burning and extruding through the "sintering" process, so as to achieve close contact between alumina particles or the formation (bonding) of long. Therefore, after sintering of ceramic green billets (green billets), weight loss, size shrinkage, shape deformation The compressive strength increases and the porosity decreases. The sintering methods of ceramic green body include: ① normal pressure sintering method, sintering without pressure will bring large deformation; ② Pressurized (hot pressed) sintering method: sintering under pressure can obtain a good flat product, which is the most adopted method at present; ③ The hot isostatic pressing sintering method is a sintering method using high pressure and high heat gas. The overall product is the product completed at the same temperature and pressure. The various properties are balanced and the cost is high. This sintering method is often used in value-added products, or aerospace, national defense and military products, such as military reflectors, nuclear fuel, gun barrels and other products.
The sintering temperature of dry pressed alumina green billets is mostly between 1200 ℃ and 1600 ℃ (related to composition and flux).
(2) Finish machining of sintered (cooked) blanks.
Most sintered ceramic blanks need to be finished for the following purposes: ① to obtain a flat surface. During the high temperature sintering process of green blanks, due to the uneven distribution of particles, voids, impurities, organic substances, etc. in the green blanks, deformation, uneven height (concavity and convexity) or excessive roughness and difference will be caused. These defects can be solved by surface finishing; ② Get a high finish surface that reflects like a mirror, or improve lubrication (wear resistance).
The surface polishing treatment is to use polishing materials (such as SiC, B4C) or diamond paste to grind the surface step by step from coarse to fine abrasive. Generally, ≤ 1 is adopted μ M of AlO powder or diamond paste, or by laser or ultrasonic treatment.
(3) Strong (steel) treatment.
In order to improve the mechanical strength (such as bending strength) of the surface after surface polishing, a layer of silicon compound film can be coated by electron ray vacuum coating, sputtering vacuum coating, chemical vapor evaporation and other methods, and the mechanical strength of ceramic blanks can be significantly improved after heat treatment at 1200 ℃~1600 ℃!
3. The conductive pattern (circuit) is formed on the substrate
To process the conductive pattern (circuit) on the ceramic substrate, first make the copper foil coated ceramic substrate, and then make the ceramic printed board according to the printed circuit board technology.
(1) Forming a copper clad ceramic substrate. At present, there are two methods to form copper clad ceramic substrate.
① Lamination method. The copper foil with one side oxidized and the alumina ceramic substrate are formed by hot pressing. That is, the ceramic surface is treated (such as laser, plasma, etc.) to obtain an activated or coarsened surface, and then laminated as "copper foil+heat-resistant adhesive layer+ceramic+heat-resistant adhesive layer+copper foil", and then sintered at 1020 ℃~1060 ℃ to form a double-sided copper clad ceramic laminate.
② Electroplating method. After plasma treatment, the ceramic substrate is "sputtered with titanium film+sputtered with nickel film+sputtered with copper film". Then, the conventional copper plating is carried out to the required copper thickness to form a double-sided copper clad ceramic substrate.
(2) Manufacturing of single and double sided ceramic PCB boards. Single and double side copper clad ceramic substrates are used according to conventional PCB manufacturing technology.
(3) Manufacturing of ceramic multilayer plates.
① The insulating layer (aluminum oxide) is repeatedly coated, sintered, wired, and sintered on the single and double sided boards to form a multilayer board, or the tape casting manufacturing technology is used to complete it.
② The ceramic multilayer plate is manufactured by tape casting method. The green strip is formed on the tape casting machine, and then the ceramic multilayer plate can be formed by drilling, plugging (conductive glue, etc.), printing (conductive circuit, etc.), cutting, laminating and isostatic pressing sintering.
Note: tape casting method - the process of making flowing glue liquid (alumina powder+solvent+dispersant+binder+plasticizer, etc. are mixed evenly+sieved)+tape casting (glue liquid is evenly coated on metal or heat-resistant polyester belt on the tape casting machine)+drying+trimming+degreasing+sintering.
In a word, ceramic PCB belongs to the category of PCB, and is also the result of the derivation and extension of the development and progress of PCB factories. In the future, it may form one of the important types in the PCB field. Because ceramic PCB has the best thermal conductive insulating medium, high melting point, thermal dimensional stability and other advantages, the application of ceramic PCB in the field of high temperature and high thermal conductivity will have broad development prospects! PCB manufacturing, PCB design and PCBA processing manufacturers will explain PCB engineers: ceramic PCB processing technology.