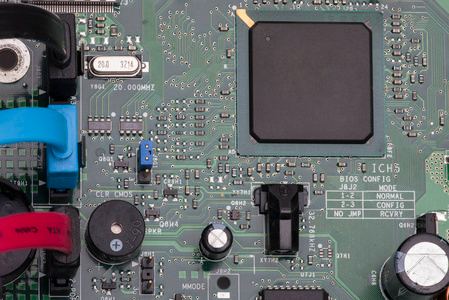
Flexible plate requirements
The miniaturization and thinness of electronic equipment inevitably use flexible PCB and rigid flexible combined PCB. The global PCB market is currently estimated at approximately $13 billion and is expected to grow at a higher annual rate than rigid PCBS.With the expansion of applications, there will be many new performance requirements in addition to the increasing number of applications. Polyimide membrane has colorless transparent, white, black and yellow and other different kinds, with high heat resistance and low CTE performance, to suit different occasions. There is also a market for cost-effective mylar substrates, where new performance challenges include high elasticity, dimensional stability, film surface quality, as well as the film's photocoupling and environmental resistance to meet the changing requirements of end users.
PCB and rigid HDI board to adapt to high speed and high frequency signal transmission requirements, the dielectric constant and dielectric loss of flexible substrate must also be paid attention to, using polytetrafluoroethylene and advanced polyimide substrate to form flexible circuit. By adding inorganic powder and carbon fiber filler to polyimide resin, a three-layer flexible thermal conductive substrate can be produced. Inorganic fillers are aluminum nitride, alumina and hexagonal boron nitride. The substrate has thermal conductivity of 1.51W/mK, can withstand 2.5kV voltage resistance, 180 degree bending test.
Printed electronics requirement
Printed electronics have been booming in recent years, with a projected market of over $300 billion by the mid-2020s. Printed electronic technology applied to printed circuit industry, is a part of printed circuit technology, this has been a consensus in the industry. Printed electronics is the closest technology to FPCB. Now PCB manufacturers have put into printed electronics. They start with flexible boards and replace printed circuit boards with printed electronic circuits . At present, there are many substrates and ink materials, once the performance and cost breakthrough will be a large number of applications, PCB manufacturers do not miss the opportunity.
Printed electronics currently focuses on low-cost manufacturing of radio frequency identification (RFID) tags that can be printed in rolls. Potential areas are printed displays, lighting and organic photovoltaics. The wearable technology market is a favorable emerging market. Wearable technology A variety of products, such as smart clothing and smart sports glasses, activity monitors, sleep sensors, smart watches, enhanced fidelity headphones, navigation compass and so on. Flexible electronic circuits are indispensable for wearable technology devices, which will drive the development of flexible printed electronic circuits.
One important aspect of printed electronics is materials, including substrates and functional inks. Flexible substrate in addition to the existing PCB circuit boards application, also developed higher performance substrate, currently there are high dielectric substrate materials composed of ceramic and polymer resin mixture, as well as high temperature substrate, low temperature substrate and colorless transparent substrate, yellow substrate, etc.
Embedded component plate requirements
Embedded component printed circuit board is a kind of product to realize high density electronic interconnection. Embedded component technology has great potential in PCB. Embedded element technology has the forming element buried method, printed element buried method, printed element is divided into thick film element and thin film element. The production of thin film components need special substrate, such as copper foil covered with nickel phosphorus alloy foil, for the production of thin film resistance; A high dielectric constant substrate is sandwiched between two sided copper-clad plates to make planar capacitors, forming a printed board with embedded passive components. There is also the development of polymer composite materials filled with ceramic powder, with high dielectric constant, low dielectric loss at high frequency, thin dielectric layer thickness, can be produced PCB circuit board inner layer RF capacitor. Embedded components are extended to flexible printed boards, and polyimide copper clad panels are also considered for making polyimide copper clad panels for film components.
Other special needs
Now, laser direct component technology has been developed for the manufacture of electronic circuits and component integrated model interconnect devices, the LDS process using thermoplastic and metal oxide materials, laser molding and circuit metallization. 3D printing technology is trying to be used in PCB manufacturing. Circuit graphics are not limited to two-dimensional planes, but become three-dimensional components. This technology also needs thermoplastic polymer materials.