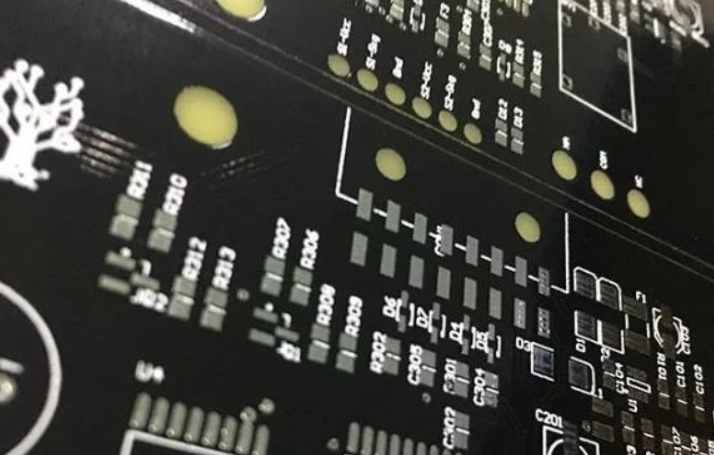
In the process of PCBA processing, we often encounter some poorly welded electronic components. Faced with this situation, we generally remove the poorly welded electronic components without damaging the PCB board. Today, Shenzhen PCBA manufacturer -kingford will introduce to you the method of dismantling PCBA.
Method of dismantling PCBA
(1) Split welding method: For horizontal installation of resistance and capacitance components, the distance between the two welding points is long, you can use the electric iron for point heating and point by point pulling out. If the pin is bent, pry it up directly with the soldering tip and remove it. When dissoldering, stand the PCB upright, heat the pin solder spot of the component to be removed with an electric soldering iron, hold the pin of the component with tweezers or needle-nose pliers, and gently pull it out.
(2) centralized diswelding method: Because the pin of the resistance is welded separately, it is difficult to heat with electric iron at the same time. A hot air welder can be used to quickly heat several solder joints, and the solder can be pulled out after melting.
(3) Stay welding method: use solder tools to absorb solder joints. In general, you can remove components. If you encounter multi - needle electronic components, you can use electronic heat fan heating.
If it is a lap-welded component or pin, you can apply flux to the solder joint, weld the solder joint with an electric iron, and remove the pin or lead of the component. If it is a hook welding component or insert needle, first use the electric iron to remove the solder at the solder joint, and then use the electric iron to heat the residual solder under the hook. At the same time, lift the pin along the hook line with the spade. Don't pry too hard so that molten solder splatters into your eyes or clothing.
(4) Shear welding method: if the pin and wire of the components on the welding spot are removed, or the components are determined to be damaged, the components or wires can be cut off first, and then cut off. Can remove the wire end of the pad.
2. Meaning of silkscreen letters on PCB board
On the PCB board, there are a lot of silkscreen letters, such as R107, C118, Q102, D202 and so on. Do you know what these letters mean? In fact, the letters on the PCB board represent the abbreviation of electronic components, in the letters are often followed by numbers, these numbers are also meaningful.
The meaning of some letters on the PCB board
B: A buzzer
C: Capacitor
D: diode
F: A fuse
J: Jumper
L: inductance
Q: Audion
R: resistor
RT: thermistor
T: Transformer
U: Chip, integrated circuit (IC)
W: Pressure regulator
Y: Crystal oscillator
R107, C118, Q102, D202 and other numbers are often seen on the circuit board. In general, the first letter identifies the device category, such as R for resistor, C for capacitor, D for diode, Q for transistor, etc.; The second is a number, representing the circuit function number, such as "1" for the motherboard circuit, "2" for the power supply circuit and so on, this is determined by the circuit designer; The third and fourth digits indicate the serial number of similar devices on the circuit board.
Shenzhen kingford Co., Ltd. specializes in providing integrated PCBA electronic manufacturing services, including upstream electronic components procurement to PCB production and processing, SMT patches, DIP plug-ins, PCBA testing, finished product assembly and other one-stop services.
The company gives full play to its competitive advantages in scale procurement and quality control, and has signed long-term cooperation agreements with many electronic component manufacturers at home and abroad and around the world to ensure the quality and stable supply of raw materials, and transfer the benefits to customers.
Long-term maintenance of IC, resistance, capacitance, inductance, audion and other components procurement advantages, can greatly save the customer's inventory cost, improve the production turnover efficiency, save time. At present, we provide PCBA processing services to customers in the United States, Britain, Japan, Russia, France, Canada, Australia, Romania, Switzerland and other countries and regions.
We provide PCBA processing services, starting from PCB circuit board production, our own PCB manufacturers (obtained the very strict TS16949 certification of the automotive industry), pay attention to the quality of the circuit board and PCBA quality control system.
Many years of experience in purchasing electronic components, and maintain long-term cooperation with large brands to ensure the original packaging and procurement channels of components. In the process of component packaging, the selection of Qianzhu and Letai solder paste, to ensure the reliability of welding, with automatic printing press, Panasonic high-speed SMT machine, up and down eight temperature zone reflow welding, AOI automatic optical detector, can effectively ensure the reliability and quality of electronic packaging process.
In addition, perfect IPC, IPQC, OQA and other management processes, clear job responsibilities, strict implementation of IPC electronic assembly acceptance standards. For PCBA testing, we have professional engineers to perform 100% batch testing using a variety of test stands, including access, noise, amplitude, signal, temperature, humidity, drop or to perform customer detailed test plans. All efforts are aimed at becoming a refined PCBA processing factory.