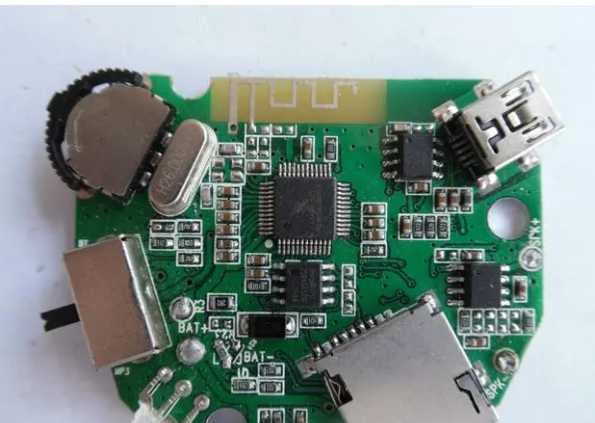
In PCBA manufacturing, automatic optical inspection is usually set at the last step of the SMT production line. After the SMT patch processing is completed, the defects of the product need to be detected. Through timely detection and reduction of defects, improve assembly efficiency and avoid material waste.
The role of automatic Optical inspection (AOI) technology in PCBA processing
The role of automatic Optical inspection (AOI) inspection
AOI is a kind of inspection equipment, also known as AOI optical automatic inspection equipment, has become an important inspection tool and process quality control tool to ensure product quality in the electronic manufacturing industry. The working principle of AOI detection equipment is that in the process of automatic detection, the AOI detection equipment machine automatically scans PCBA products through the high-definition CCD camera, collects images, compares the test point with the qualified parameters in the database, checks out the solder spot defects on the target PCBA after image processing, and displays or automatically marks the defects. Improve process parameters for maintenance personnel and SMT technicians.
The AOI system includes multiple light sources, high-speed digital cameras, high-speed linear motors, precision mechanical transmission structures and image processing software. Test, AOI equipment through the camera automatically scan and PCB, PCB parts or special parts (including the state of the printed solder paste, SMD components, solder joint shape and defects) to capture the image, through processing and database software to compare the qualified parameters, and comprehensive judgment components and characteristics are qualified, and then test the conclusion, Such as missing components, bridge or solder joint quality problems.
AOI works in the same way as the visual systems used in SPI and printing presses in SMT, typically using design rule checking (DRC) and pattern recognition. The DRC method checks the circuit pattern according to some given rules (all wires should end at the solder joint, all leads should be at least 0.127 mm wide, all leads should be at least 0.102 mm apart, etc.). This method can guarantee the correctness of the circuit to be tested algorithmically, and has the characteristics of simple production, simple algorithm logic, fast processing speed, small amount of program editing, and small data space, so it is adopted by many people. But this method has poor ability to determine the boundary.
The pattern recognition method is to compare the stored digital image with the actual image. Check according to the complete printed circuit board or according to the test documents established by the model, or according to the test procedures prepared in the computer shaft aided design. Its accuracy depends on the licensing rate and inspection procedures adopted. It is generally the same as the electronic test system, but the amount of data collected is large and the requirement for real-time data processing is high. The pattern recognition approach, which uses actual design data to replace established design principles in DRC, has obvious advantages.
AOl has components testing, PCB board testing, welding components testing and other functions. The general procedure of AOI inspection system for parts inspection is to automatically count the printed circuit board of the installed parts and start the inspection; Check the lead side of the printed circuit board to ensure that the lead end is aligned and bent correctly. Check for missing, wrong, or damaged parts. Check the type, direction, and position of the installed IC and discrete devices. Check the printing quality of the labels on the IC devices. If AOI finds a defective part, the system sends a signal to the operator, or triggers a handler that automatically removes the defective part. The system analyzes defects, provides the type and frequency of defects to the main engine, and makes necessary adjustments to the manufacturing process. The efficiency and reliability of AOI testing depends on the integrity of the software used. AO also has the advantage of being easy to use, easy to adjust, and not requiring you to write a visual system algorithm.
Our PCBA processing advantage
Shenzhen KIkingford own SMT processing plant, can provide minimum package 0201 components SMT processing services. The SMT plant is equipped with 3 Fuji high-speed SMT production lines, 2 DIP plug-in production lines, including AOI optical detector, automatic solder paste printing machine, semi-automatic solder paste printing machine, lead-free wave soldering, lead wave soldering, upper and lower 8 temperature zone reflow welding, PCBA functional testing frame, aging, plate loading machine, cleaning tools, etc., and a professional research and development laboratory is also set up. Five professional engineers cooperate with customers to conduct general function testing, test point testing, as well as channel, noise, waveform, drop and temperature testing.
The company specializes in providing overall PCBA electronic manufacturing services, including upstream electronic components procurement to PCB production and processing, SMT patches, DIP plug-ins, PCBA testing, finished product assembly and other one-stop services.