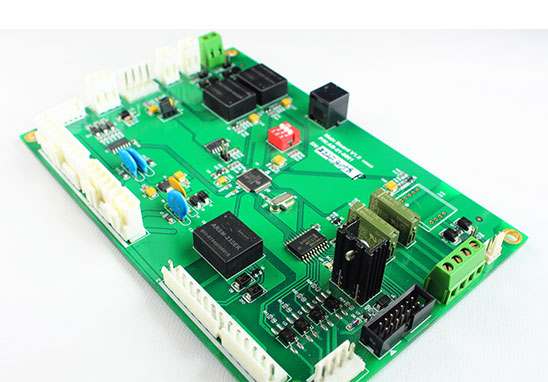
PCB DIP plug-in processing is a very important process in PCBA patch processing, and its processing quality directly affects the functional properties of PCBA board, so it is necessary to pay more attention to the DIP plug-in process. The basic process of DIP plug-in is to process the electronic components of the plug-in first. The staff will receive the materials according to BOM, check whether the material models and specifications are correct, and conduct pre-processing according to PCBA template before production. The step is to use a variety of related equipment (automatic capacitance pin clipper, jumper bending machine, two and three audion automatic forming machine, automatic belt forming machine and other forming equipment) for processing.
PCB DIP plug-in processing needs to pay attention to the following points:
1. Before plug-in, it is necessary to check whether the surface of electronic components has oil stains, paint and other unclean objects.
2. In the plug-in process, it is necessary to ensure that the electronic components are flat with PCB. After the plug-in is completed, it is necessary to ensure that the electronic components are in a flush state, not uneven, and ensure that the welding pins after the plug-in cannot block the welding pad.
3. If there is a direction indicator on the electronic components, it is necessary to plug in the correct direction. Do not plug in at will.
4. Pay attention to the force of the plug-in when installing the plug-in. Do not use too much force when installing the plug-in, which may cause damage to components or PCB board.
5. Do not plug out the edge of PCB board when inserting electronic components. Pay special attention to the height of electronic components and the spacing between electronic components.
2. Matters needing attention in PCB proofing etching process
In PCB proofing, the copper foil part is pre-coated with a layer of lead tin anticorrosive layer, which remains in the outer layer of the board, that is, the graphic part of the circuit, and then the rest of the copper foil is chemically etched, known as etching.
As PCB from light board to display circuit graphics last process, etch should pay attention to what quality problems? Next, Shenzhen PCB proofing manufacturer -kingford will introduce the precautions of PCB proofing etching process.
The quality requirement for etching is the complete removal of all copper layers beneath the anticorrosive layer. Strictly speaking, the etching quality must include the consistency of linewidth and the degree of lateral erosion.
The problem of side etching is often discussed in etching. The ratio of side etching width to etching depth is called the etching factor; In the printed circuit industry, small side etching or low etching factor is most satisfactory. The structure of the etching equipment and the different composition of the etching solution will affect the etching factor or the degree of side erosion.
In many ways, the quality of the etching exists long before the board enters the etching machine. Because there is a very close internal relationship between each process of PCB proofing, no process is not affected by other processes. Many of the problems identified as etch quality have actually existed in previous film removal processes, and more.
In theory, PCB proofing enters the etching stage. In pattern plating, the ideal condition should be that the total thickness of the copper and lead tin after plating should not exceed the thickness of the plating resistant photosensitive film, so that the plating pattern is completely blocked and embedded by the "wall" on both sides. But in the actual production, the plating pattern is much thicker than the photographic pattern; Because the coating height exceeds the sensitive film, there is a trend of lateral accumulation. A tin or lead tin corrosion resistant layer covering the line extends to the sides to form the "edge", covering a small portion of the sensitive film below the "edge". The "edge" formed by tin or lead tin makes it impossible to completely remove the sensitive film when removing the film, leaving a small part of the "residual glue" below the "edge", resulting in incomplete etching. The etched wires form "copper roots" on both sides, narrowing the spacing between the wires, resulting in printed boards that fail to meet customer requirements and may even be rejected. Waste products will greatly increase the cost of PCB production.
In PCB proofing, once there is a problem in etching process, it is bound to be a batch problem, which will eventually cause a great quality hazard to the product. Therefore, it is particularly important to find suitable PCB proofing manufacturers
Shenzhen kingford own SMT processing plant, can provide minimum package 0201 components SMT processing services. The SMT plant is equipped with 3 Fuji high-speed SMT production lines, 2 DIP plug-in production lines, including AOI optical detector, automatic solder paste printing machine, semi-automatic solder paste printing machine, lead-free wave soldering, lead wave soldering, upper and lower 8 temperature zone reflow welding, PCBA functional testing frame, aging, plate loading machine, cleaning tools, etc., and a professional research and development laboratory is also set up. Five professional engineers cooperate with customers to conduct general function testing, test point testing, as well as channel, noise, waveform, drop and temperature testing.
We can provide one-stop PCBA OEM service from upstream electronic components procurement to PCB production and processing, SMT patches, DIP plug-ins, PCBA testing and finished product assembly.