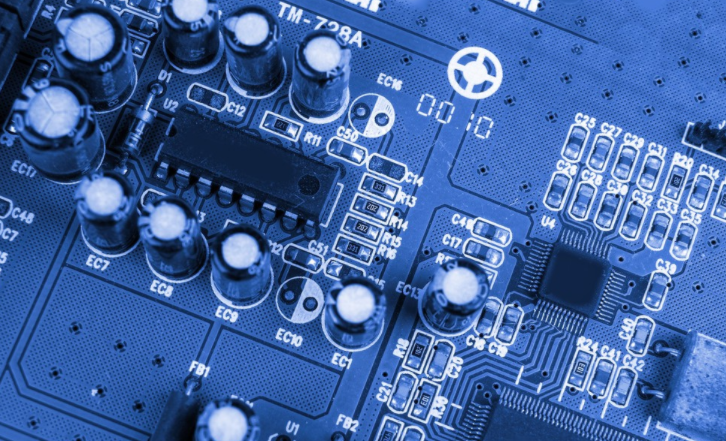
PCBA assembly priority inspection advantages
The vast majority of factories must take an important step towards this goal and conduct the first inspection At the beginning, the factory and the customer inspected for the first time As time goes on and accumulates, the factory has higher and higher requirements for product output and quality The first inspection was started to eliminate defects in the early stage of production. After all, the first inspection process occurred The customer also agreed For the most basic product PCBs, the first inspection is an essential and important link This ring saves energy, saves costs and increases production
First inspection. Jpg company
Significance of the first inspection
This first batch or previous batches belongs to products produced after each shift/the production line is put into operation
The test is divided into several types:
1 Visual inspection
2. False welding inspection
3. Check the accuracy of the placement of components
4. Are there any missing parts
5. The most basic check, such as patch offset
This work is also called the first inspection because it is a specific sample collected before mass production, so it is also called the first inspection.
Generally speaking, the first inspection requires that the product be inspected and put into mass production after passing the inspection. This is the link that traditional PCB manufacturers will follow, and its purpose is self-evident.
Advantages and Importance of the First Inspection of PCBs
In order to prevent poor quality, maintenance or massive scrapping of products in the production process, PCB manufacturers will conduct the first inspection in advance
First inspection personnel
The advantages are reflected in three aspects:
1. Avoid wasting resources
Because the first inspection belongs to polychlorinated biphenyl plate, which is inferior, maintenance and scrapping of a large number of products are avoided Therefore, we can make better use of resources without wasting a lot of resources This is a kind of cost control for enterprises, which can reduce investment costs for PCBs manufacturers and electronic enterprises
2. Quality control
The first inspection of PCBs is an effective means to control the production process in advance. It can control product quality, help enterprises to better determine the production quality of these products, and improve the economic benefits of enterprises.
3. Improve corporate reputation
No matter how good the quality is, there is much waste and low success rate in the production process. Such PCB manufacturers are not what electronic enterprises want. In order to improve its image and reputation, PCB manufacturers will control product quality, success rate, qualification rate and high quality rate. When these data exceed the standard, they will have a good reputation in the industry and attract more customers to cooperate.
importance:
The importance of first inspection of PCBs is also reflected in the cost At the same time, it can also improve production efficiency and reduce enterprise cost investment Both PCBs manufacturers and electronic enterprises will get more profits If enterprises want to attract customers through price reduction promotion, they need not worry about losing money
In conclusion, the first inspection of PCB plates is very important and must be paid attention to. As a PCBA manufacturer, the first inspection is of great significance. As an electronic enterprise, the first inspection can help enterprises better understand the situation of cooperative manufacturers, which is very helpful for future cooperation and development.