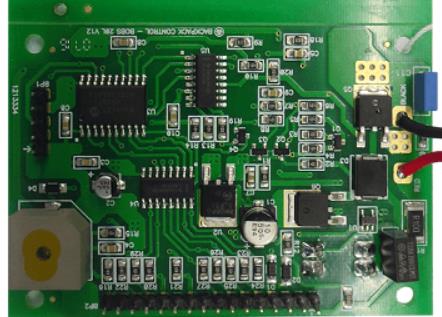
Cleaning requirements for dust-free workshop after SMT chip processing and welding
Cleaning after SMT processing and bonding PCBs processing plant refers to the removal of SMT reflow welding, the use of physical effects and chemical reaction methods, after peak welding and manual welding, the residual solder on the surface layer of the surface layer, as well as pollutants generated during SMT processing and assembly, and the hazards of pollutants in the process flow to the surface assembly plate
1. The activating agent and solder sound added in the solder contain a small amount of westernized substances, acids or salts, resulting in residual impurities covering the SMT solder joint surface. When the electronic equipment is powered on, the residual impurity ions will migrate to the conductor with opposite polarity, which may cause short circuit in serious cases.
2. Halogen in the current common solder, chloride has a strong activity and moisture absorption. In the humid environment of Hunan Province, they will corrode the substrate and solder joints, reduce the insulation resistance of the substrate surface, and generate electric migration. When the situation is serious, they conduct electricity and cause short circuit or open circuit.
3. The polychlorinated biphenyl factory shall carry out SMT processing for the products with special requirements such as high standard military products, medical products, instruments and meters, and shall carry out three prevention treatment. 3 The standard before anti treatment has a high degree of cleanliness, otherwise under relatively adverse environmental conditions, such as hot flashes or high temperatures, serious consequences, such as reduced or invalid power efficiency, will be caused.
4. Due to the rapid mask of residual impurities after welding, the probe for online or functional time measurement is not well contacted, which is easy to make mistakes.
5. For high standard products, SMT cannot expose defects such as thermal damage and spalling due to the mask of post welding residues, resulting in leakage and affecting reliability. At the same time, more impurities also affect the appearance of the base plate and the products of the plate.
6. Post weld debris will affect the connection reliability of high-density, multi input/output junction array wafers and reverse wafers.
Generally speaking, SMT processing workshops have several requirements for a dust-free environment. First of all, the bearing capacity, vibration and noise requirements of the workshop, the bearing capacity of the workshop pavement should exceed 8KN/m2, the vibration should be controlled within 70dB, and the maximum value should not exceed 80dB.
Polychlorinated biphenyls
SMT processing workshop needs air supply. Air supply pressure shall be provided according to equipment requirements. It can use the air source of the factory. Oil free compressed air machine can also be equipped separately. Generally, the pressure is greater than 5kg/cm2. Clean and dry purified air is required. In this case, the compressed air must be degreased, dedusted and treated with waste water, and the stainless steel plate or pressure resistant plastic hose must be used as the gas pipe. There is also a requirement for the exhaust system, and the equipment of the reflow welding replacement factory furnace and peak welding machine needs to be equipped with an exhaust fan.
The SMT processing workshop must be kept daily clean, free of dust and corrosive steam. The production workshop needs to conduct cleanliness control. The cleanliness control is Class 500000. The optimal working temperature of the production workshop is 23+3 ℃, generally 17-28 ℃, and the air humidity is 45% - 70% RH. According to the specifications and dimensions of the production workshop, a suitable thermometer and hygrometer should be set for regular supervision. It is equipped with equipment to adjust temperature and humidity.