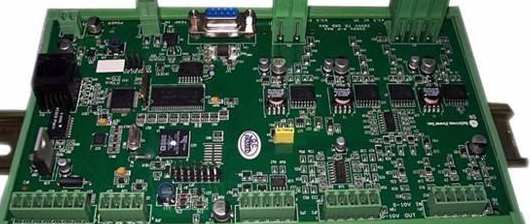
Why do I need to pre-heat PCBA before processing?
Quality control is a very important link. If we can effectively carry out quality control, then we can ensure that the final product we produce is of high quality, which is very important for our customers and consumers. In this article, we will explore how to do quality control in PCBA processing.
First, we need to understand what PCBA processing is. PCBA is the abbreviation of Printed Circuit Board Assembly, that is, printed circuit board assembly. It is a very important part of our electronic products, including the assembly and welding of circuit boards. The process of PCBA processing is very complex and requires a high degree of precision and technical requirements. Therefore, we need very strict quality control during PCBA processing.
In the PCBA processing process, we need to pay attention to the following aspects:
1. Selection of materials In the PCBA processing process, we need to choose high-quality materials. These materials need to meet our equipment requirements to ensure that the quality of the products we manufacture is at a high level. At the same time, we also need to choose reliable material suppliers to ensure that we can obtain high-quality materials.
2. Process control In the PCBA processing process, process control is very important. We need to make sure that every step is carried out according to the standard and that nothing goes wrong in the production process. This is very important to ensure that the quality of our products is at a high levelhttps://www.kingfordpcb.com/yuan.php
3. Equipment maintenance PCBA processing requires the use of a large number of equipment and machines, so the maintenance of equipment and machines is also very important. We need to regularly inspect and maintain our equipment and machinery to ensure that they are functioning in optimum condition. This helps to ensure that our products meet the requirements of our customers.
4. Quality testing Quality testing is one of the important means to ensure that the quality of the products we produce is high. We need to conduct quality inspection at each step and a final inspection of the entire product before the final product leaves the factory. This helps us identify any potential problems and resolve them in a timely manner.
5. Staff training In the PCBA processing process, the skills and experience of employees are also very important. We need to train our employees regularly to ensure they are up to date with the latest processes and technologies. This helps to improve the technical level and productivity of employees.
In the process of PCBA processing, the above aspects are very important. We need to pay attention to these aspects to ensure that the product we end up producing is of a high level of quality. At the same time, we also need to constantly sum up experience in actual production and constantly improve the quality control process.
It is an important electronic manufacturing industry, which involves many links and steps. Preheating is a key step in PCBA processing. So why do you need to pre-heat PCBA before processing? This article will explore this issue in detail.
1. What is PCBA? Before discussing why pre-heating is necessary, we need to understand the concept of PCBA. PCBA refers to the assembly of components on a printed circuit board so that they can perform specific functions. PCBA is a very important manufacturing area because modern electronic devices cannot live without printed circuit boards. Due to the low cost, small size and wide use of printed circuit boards, in addition to traditional electronic products, they are now widely used in smart home, smart wear and other fields. The manufacturing process of printed circuit board is very complex, involving a variety of technologies and processes.
2. Pre-heating in PCBA processing
In the PCBA process, pre-heating is a very important step. So, what is preheating? Pre-heating refers to a process in which the PCB board is heated on a special heating table before PCBA processing, and the following effects can be achieved through heating:
- Drive away surface moisture: Before PCBA processing, PCB board will always be exposed to the air, so the surface will produce a lot of moisture. If these moisture is brought into the processing process, it will have an impact on welding, plating and other processes. By pre-heating the PCB before processing, the surface moisture can be driven away to ensure that its surface is dry.
- Preheat PCBA components: PCBA components due to long-term storage, transportation and other factors, will make its surface attached to a lot of impurities. If these impurities are brought into the processing operation, it will adversely affect the quality of components, spot welding, patch and other processes. By preheating the components, impurities can be removed, and their own characteristics can be restored to improve the quality of subsequent processing.
- Prevent PCB welding rupture: During welding, due to the relatively large temperature change of PCB board, it will cause the board to shrink or expand, and this difference can lead to the rupture of PCB welding. Through pre-heating, the PCB board can be uniformly warmed to achieve the purpose of more stable welding.
- Improve the precision of PCBA processing: When performing patch and spot welding, high temperatures help speed up the welding process, improve viscosity and strength, and ensure accuracy. Pre-heating can keep the PCB at a constant temperature during processing and ensure the accuracy of processing.
3. Precautions for pre-heating
In the process of pre-heating, special attention should be paid to the following:
- Temperature: The pre-heating temperature should not be too high, otherwise it may cause damage to the PCB or PCBA components. Under normal circumstances, the pre-heating temperature is about 100-120 degrees.
- Time: the pre-heating time is too long or too short is not good, too long will saturate PCBA components, overheating for too long may lead to discoloration and blackness, and too short time can not achieve the preheating effect. The pre-heating time is generally between 2-5 hours.
- Effect: The pre-heating effect must be achieved, and can play a due role in the subsequent processing, if the effect is not ideal, it is necessary to reheat.
- Operator: Although pre-heating is not difficult, improper operation can easily cause damage to PCBA components, thereby affecting product quality. Therefore, the operator must have a certain amount of process operation experience. 4. Closing remarks
In summary, preheating is an indispensable part of PCBA processing. Through pre-heating, moisture can be driven away, PCBA components can be preheated, PCB welding can be prevented, processing accuracy can be improved, etc., to ensure the smooth process of PCBA processing, and high quality electronic products can be produced. If you are also engaged in related fields, be sure to strictly follow the pre-heating operating procedures to ensure the stability and quality of the product, and make a positive contribution to the development of the electronics manufacturing industry.