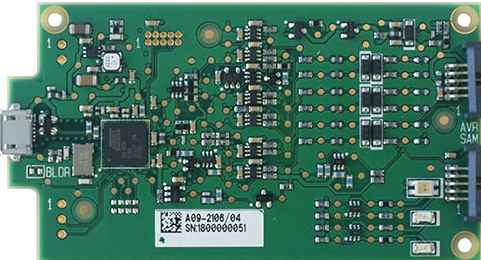
How to select the PCBA substrate type?
It is an important part of the manufacturing process of electronic products, and choosing the right PCBA substrate type is crucial to product performance and quality. The selection of a PCBA substrate type involves several factors, including application areas, cost, performance requirements, and manufacturing processes.
1. Rigid PCB
Rigid substrates are one of the most common types of PCBA substrates, which are made of hard materials such as FR4 and have excellent mechanical strength and stability. Rigid substrates are suitable for most electronic devices, such as computers, communications equipment and consumer electronics. They can carry complex circuits and components and provide stable electrical performance. The manufacturing process of the rigid substrate is mature, the price is relatively low, and it is suitable for middle and high-end electronic products.
2. Flexible PCB
The flexible substrate is a PCBA substrate made of a flexible material with excellent bending and folding properties. They are typically thinner and lighter than rigid substrates and are suitable for applications that require high weight and volume, such as mobile devices, wearables and automotive electronics. Flexible substrates can be wired in three-dimensional space and can be bent and folded, providing greater design freedom. However, the manufacturing process of flexible substrates is more complex and costly.
3. Rigid-flex PCB (Rigid Flex PCB)
Rigid and flexible bonded substrate is a combination of rigid substrate and flexible substrate, which has the advantages of both. It is composed of rigid and flexible layers stacked cross-over, which can meet the complex wiring needs to a certain extent, and provide flexability. Rigid and flexible substrates are widely used in applications that require both rigid and flexible connections, such as folding mobile phones, medical devices, and aerospace electronics. However, the process of manufacturing rigid-flexible bonded substrates is more complex and relatively expensive.
4. High Density Interconnect substrate (HDI PCB)https://www.kingfordpcb.com/yuan.php
A high density interconnect substrate is a PCBA substrate that achieves high density wiring over a relatively small area. It uses fine line width, line spacing and through holes to achieve higher component density and better signal transmission performance. HDI PCBS are suitable for applications that require high-speed signal transmission and miniaturized design, such as mobile devices, high-performance computers and communication equipment. Because the manufacturing process of HDI PCBS is more complex, its cost is relatively high.
5. RF Substrate (RF PCB)
Rf substrates are PCBA substrates specially designed for RF signal transmission and processing. They use special materials and wiring technology to ensure stability and low loss in the high frequency range. Rf substrates are widely used in wireless communication, radar system and satellite communication. Due to their special design requirements and material selection, RF substrates are relatively expensive to manufacture.
6. Metal Core PCB
A metal substrate is a PCBA substrate which is coated with a metal layer on the surface of a rigid substrate. This substrate can provide excellent thermal performance and is suitable for applications that need to handle high power and high temperatures, such as LED lighting, power modules and automotive electronics. Metal substrate has good thermal conductivity and mechanical strength, but is relatively expensive to manufacture compared to other substrate types.
7. Thick Copper PCB
Thick copper substrate is a PCBA substrate with a high copper layer thickness. They are suitable for applications that need to handle high currents and high power, such as electric vehicle battery management systems, industrial control equipment and power supply systems. Thick copper substrates can provide low resistance and good heat dissipation performance, but their cost is higher due to special manufacturing processes and material requirements.
By understanding the different types of PCBA substrates and their characteristics, we can choose the right type for our specific needs. Factors to consider include application areas, cost budgets, performance requirements, cabling complexity, and manufacturing processes. When selecting a PCBA substrate, it is best to work with a professional PCBA manufacturer to ensure that the type of substrate selected meets the product needs and meets high quality manufacturing standards.
The choice of PCBA substrate type is critical to the performance and quality of the product. Rigid substrates are suitable for most applications, flexible substrates are suitable for thin and flexible designs, rigid and flexible substrates are suitable for complex rigid and flexible connection needs, HDI PCBS are suitable for high density wiring, RF substrates are suitable for RF signal processing, metal substrates are suitable for heat dissipation performance requirements, and thick copper substrates are suitable for high current and high power applications. According to the specific needs and application scenarios, selecting the appropriate PCBA substrate type will help ensure the performance, reliability and stability of the product.
In addition to selecting the right PCBA substrate type, other factors should be considered to optimize the PCBA design and manufacturing process. For example, reasonable layout of circuit components and signal lines to reduce interference and signal loss; The use of high-quality electronic components and welding processes to ensure stable electrical connections; Strict quality control and testing is carried out to ensure the reliability and quality of PCBA.
In short, choosing the right PCBA substrate type is an important step in ensuring the performance and quality of electronic products. Different substrate types are suitable for different application requirements and need to be selected according to comprehensive considerations. Working with a professional PCBA manufacturer, you can get professional advice and support to ensure the success of PCBA design and manufacturing. Through reasonable substrate selection and optimized design process, high quality and high performance PCBA assembly can be achieved to meet market demand and user expectations.