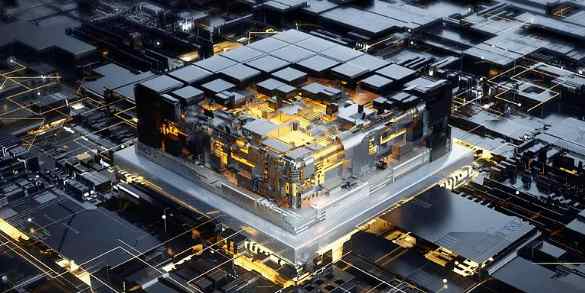
(1)Telephus
IPD developed by Telephus uses a thick copper process that improves performance, reduces cost and reduces size for lines with only passive components, such as filters and transmitters, thick copper layers (10mm) and silicon insulated surfaces that enable high performance for wireless communication systems and integrated RF modules. The low dielectric constant material is suitable for reducing the parasitic capacitance between metal layers, and its IPD structure is shown in Figure 2.
(2)IMEC
IMEC's thin film technology also uses electroplated copper as the connecting line, BCB as the dielectric layer, Ni/Au layer as the final connecting surface metal, using up to 4 layers of metal layers. Its IPD structure is shown in Figure 3.
(3)Dai Nippon
The IPD resistance developed by Dai Nippon is mainly Ti/Cr, the capacitor adopts the process of anodizing to form Ta2O5, and the inductance design is composed of microstrip wire and spiral inductance, and the circuit is mainly copper, as shown in Figure 4.
(4)SyChip
The IPD developed by SyChip takes TaSi as the resistance material, the dielectric material of the capacitor is Si3N4, the power-on electrode is Al, the power-off electrode is TaSi, and the inductor and line material are both aluminum, as shown in Figure 5.
The impact of integrated passive components on PCB technology development
There are some companies that are adopting MEMS processes to develop IPD, such as PHS MEMS, which explains that the method for manufacturing MEMS components basically comes from the IC industry. At the same time, some established companies in the development of relevant technologies at the same time, but also through acquisition and other means to obtain the market and technology, such as Murata (Murata) acquired SyChip company, hoping to expand its share in the RF application market through the acquisition.
4 Structure and process of thin-film integrated passive element technology
The biggest difference between the film process and the thick film process is the film thickness generated, the general so-called thick film thickness is more than 5μm ~ 10μm, and the film thickness generated by the film process is about 0.01μm ~ 1μm.
If the use of thin film process at the same time to form resistance. Capacitance. The components of inductors need to be made with different processes and materials. Thin film technology is used in semiconductor integrated circuit manufacturing process, the technology development has been quite mature, so in the process integration, only need to pay attention to the compatibility of materials between different components, you can achieve the design of the process.
Overall, the thin-film IPD integrates passive components and can be manufactured on different substrates for different product applications, and the substrate can be selected as a silicon wafer. Alumina ceramic substrate. Glass substrate. Thin-film IPD integrated passive element technology can integrate thin-film resistors. Capacitors and inductors are integrated, and its process technology is developed, including: micro image processing technology. Film deposition processing technology. Etching processing technology. Electroplating processing technology. Electrodeless electroplating processing technology, the entire processing flow is shown in Figure 6. In addition to the integration of passive components, the process of active components can also be combined on silicon wafers to integrate passive components and active component circuits to achieve multi-functional needs. Here's the thin film resistor. The machining of capacitors and inductors is briefly introduced.
(1) Film resistance processing
The production method of thin film resistor usually uses sputtering process, the resistance material is electroplated on the insulating substrate, and then the resistance pattern is processed to obtain the designed resistance value by using the technology of photoresistance and etching. The process diagram is shown in Figure 7.
In the application of materials, it is necessary to consider the TCR of the resistance material, that is, the resistance change rate at different temperatures. Thin film resistance is formed by vacuum evaporation. Sputter. Thermal decomposition and electroplating, while commonly used resistance materials contain a single component metal. Alloys and cermet three.
(2) Film capacitor processing
Because MIS(metal-Insulator-Semiconductor metal-insulator - semiconductor structure) thin film capacitor uses the semiconductor as the bottom electrode, so that the capacitor itself has parasitic resistance, resulting in the reduction of the resonance frequency of the component, which can not be applied to the rate above 200 MHz. Therefore, the application of high frequency must choose MIM(metal-insulator -metal - semiconductor structure) film capacitor, MIM capacitor can reduce the parasitic resistance value, and then improve the resonance frequency of the component, and the resonance frequency is determined by the natural vibration frequency of the dielectric material. Like thin film resistors, thin film capacitors need to consider the capacitance change rate, and the dielectric constant also needs to be considered, and its manufacturing process diagram is shown in Figure 9.
In addition, attention should be paid to the surface roughness of the substrate. 0.3μm, if the roughness Ra value exceeds the specified range, the dielectric layer is easy to be penetrated by the Hill Lock of the bottom electrode, forming a short circuit.
(3) Thin film inductance processing
The film inductance process is similar to the resistance process, but the main design consideration is how to reduce its parasitic capacitance and improve the quality factor (Q) of the component, due to the inductance characteristic ratio, considering the need to reduce its DC impedance to improve the Q value, so the film thickness of the inductor wire must be between 5μm and 10μm. Therefore, electroplating is usually used in the process to form inductance wires to meet the demand.
The surface roughness of the substrate will affect the characteristics of the film inductance, especially at high frequency, too high surface roughness is easy to cause the increase of noise, resulting in the reduction of high frequency characteristics, so the selection of the substrate, production, and processing will affect the performance of the entire film element.