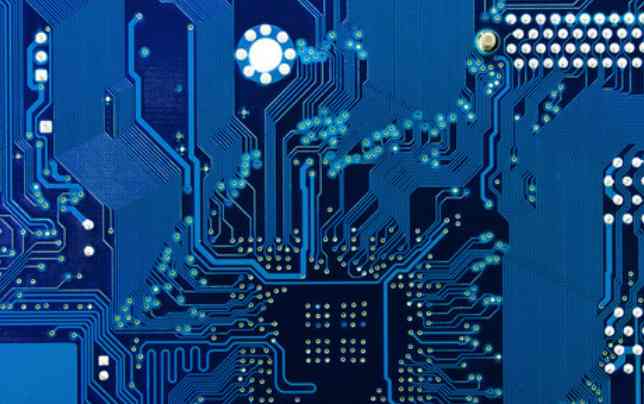
The situation involving the moisture sensitivity of plastic integrated circuits (ics) is gradually getting worse due to a number of industrial trends, including the increasing search for more reliable products to support critical communications and technology applications. The failure rate of MSD (moiSTure-sensitive device) alone is already at an intolerable level, coupled with the continuous change of packaging technology. Shorter development cycles, shrinking sizes, new materials and larger chips are causing rapid growth in the number of MSDS and higher levels of moisture/reflux sensitivity. Finally, the growing use of area-aligned packages such as BGA and CSP has also had a significant impact. This is because these components tend to be packaged in tape-and-reel systems, with a large number of components per reel. When compared with the pin element in the IC tray, the key issue is the longer exposure to moisture.
The effects of external processing
Perhaps the most important factor is the growth of contract manufacturers and mass customization. In the printed circuit board manufacturing industry, this becomes a "highly mixed" production, where the reduction in batch volume leads to more product conversion on the assembly line, resulting in an increased exposure time to MSDS. Each time the SMT line is converted to a new product, most of the components already loaded on the mounting machine have to be removed, resulting in many parts of the pallets and tape that need to be temporarily stored for later use. The MSD thus stored is likely to exceed its critical moisture content before returning to the assembly line and the final soldering reflux process. Therefore, during setup and handling, the exposure time must be increased to the dry storage time.
IPC/JEDEC standard
The guidelines for classification, handling, packaging, transportation, and use of MSDS are clearly defined in industry standard J-STD-023, a joint publication of the American Electronics Industry Federation (IPC) and the Welded Electronic Components Engineering Council (JEDEC). This document was issued in 1999 and mainly harmonized and revised two previous standards: IPC-SM-786 and JEDEC-JESD22-A112(both of which are now obsolete). The new standard contains a number of important additions and changes that must be followed to update existing manufacturing systems and procedures.
All in all, the standard requires MSDS to be properly sorted, labeled, and packaged in dry bags until they are ready for PCB assembly. Once the bag is opened, each component must be assembled and reflow welded within a specified time frame. The standard requires that the total cumulative exposure time of each roll or reel of MSD should be tracked through the complete manufacturing process until all parts are mounted. Proper supply of materials should effectively reduce the exposure time during storage, preparation, and implementation. In addition, the standard provides flexibility to increase or decrease the maximum production life, based on indoor environmental conditions and baking time.
Manufacturing process overview
While the principle of assembling an MSD within a specified production life may sound like a straightforward requirement, practical implementation in a production environment is always challenging. Because standards are sometimes misunderstood (and there is no easy way to do what is required), there is a big difference between the actual manufacturing procedures in the factory and the factory. For example, there are companies that simply do not have documented manufacturing procedures to track and control MSDS. Instead, some companies have built systems that are so cumbersome that they consume so much time and energy that production operators are nearly impossible to follow.
In between these extremes, most companies set up workable, simplified working procedures with many assumptions. However, this results in the assembly of those components that need to be baked and the unnecessary parts are baked together. The first will affect material availability, weldability, and lead to the waste of expensive components. Other conditions will affect the reliability of the final product. Unfortunately, in many organizations, MSD working procedures were established many years ago and are not regularly revised. Changes in components, product mix, material supply, assembly processes, equipment and standards are not reflected, and therefore their effectiveness is greatly compromised.
The identity of MSD
The first issue related to MSD control is the identification of trays and reels. Once removed from their protective drying bags, how are these trays and reels with components identified? If the component is not received in a drying bag, or if the bag is not properly identified, there is a risk that it may be treated as a non-moisture sensitive component. Material handlers and operators must have a convenient and reliable way to confirm part numbers and related information, including moisture sensitivity levels.
The majority of MSDS are packaged in plastic IC drag-trays that conform to the standard JEDEC/EIAJ form factor. Unfortunately, these trays don't have surface space to label them. In most cases, individual trays are identified indirectly, with paper or labels placed on shelves, machine feeders, drying chambers, bags, etc. All data must be transferred from the original label through different steps. Those who have spent any amount of time on SMT production lines know the great difficulties caused by tracking the components packed in trawles, and the resulting human error.