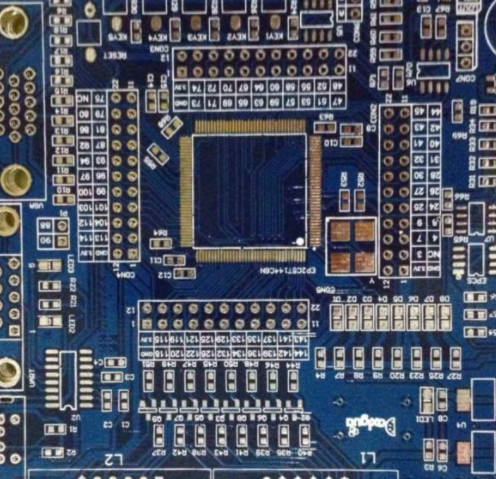
Electrolytic cleaning method of PCBA board
Before pcba manufacturing and pasting the dry film, the surface of the substrate is generally cleaned using the above two treatment methods (1) and (2). Mechanical cleaning and pumice plastering are good for removing the chromium containing passivation film (copper foil surface antioxidant) on the surface of the substrate, but it is easy to scratch the surface, and may form abrasive particles (such as silicon carbide, aluminum oxide, pumice powder) embedded in the copper substrate. pcba manufacturers are used for flexible substrate The cleaning of the inner layer of multilayer board and thin printed board substrate is easy to deform the size of the substrate. Chemical cleaning has good degreasing property and will not deform the flexible board or thin substrate. However, it is not as effective as mechanical cleaning in removing the chromium containing passivation film on the copper surface.
The advantage of electrolytic cleaning in pcba circuit board manufacturers is that it can not only better solve the problems of mechanical cleaning, pumice plastering and chemical cleaning on the surface of the substrate, but also make the substrate produce a relatively uniform micro rough surface , greatly improve the specific surface, and enhance the adhesion between the dry film and the surface of the substrate, which is very beneficial to the production of high-density, thin conductor conductive patterns.
Substrate surface state with different treatment methods
The process of electrolytic cleaning is as follows: feeding → electrolytic cleaning → water washing → micro etching → water washing → passivation → water washing → drying → discharging
The main function of electrolytic cleaning is to remove oxides, fingerprints, other organic contaminants and chromium containing passivates on the copper surface of the substrate, and to have a micro etching effect on the copper surface, so as to form a micro rough surface on the copper surface to increase the specific surface. To prevent the cleaned surface from oxidation, it shall be passivated to protect the roughened fresh copper surface. Electrolytic cleaning is mainly used to clean the surface of flexible substrate, multilayer board inner layer and thin printed board substrate before sticking dry film or coating liquid photoresist. Although it has many advantages, it is ineffective for cleaning epoxy stains on copper surface, and the cost of wastewater treatment is also high.
It is reported that Atotech Inc. (Chemeut) of the United States has launched the CS - 2000 series of horizontal anode electrolytic cleaning equipment in the early 1990s, and also sells Scherclean ECS series of electrolytic cleaning agents. Whether the pcba production treated panel is clean or not should be checked. a simple inspection method is water wettability inspection (also known as water film rupture test). The specific method is to soak the board with running water and place it vertically after the board surface is cleaned. The continuous water film on the whole board surface shall be able to maintain for 15s without cracking. It is better to apply film immediately after cleaning treatment to prevent re oxidation of the surface. If the storage time exceeds 4h, it shall be cleaned again.
An American company used radioactive ester acid to measure the surface area of copper substrate before and after cleaning treatment. It was found that the surface area of copper substrate after treatment was three times larger than that before treatment. It was precisely because of the existence of a large number of micro rough surfaces in the pcba patch processing plant that under the condition of film heating and pressure, the corrosion inhibitor flowed into the microstructure of the substrate surface, greatly improving the adhesion of the dry film. The drying of the board surface before film application is very important. The residual moisture is often one of the reasons for sand holes or poor film application. Therefore, the moisture in the board surface and holes must be removed to ensure that the board is dry during film application. It is usually removed by physical methods, such as air knife drying. If the plate surface and hole are still not dry, put them into a 110 ℃± 5 ℃ hot oven for thermal evaporation for 10~15min. To avoid cross contamination of the board surface, the oven shall be a special equipment.