Building 6, Zone 3, Yuekang Road,Bao'an District, Shenzhen, China
+86-13923401642Mon.-Sat.08:00-20:00
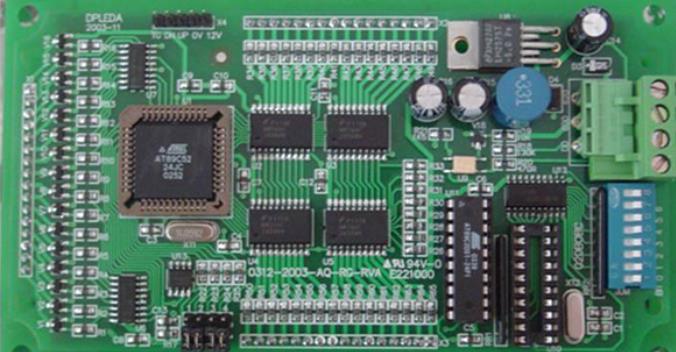
Basic requirements for SMT component layout design
The layout of components shall be based on SMT wafer processing production equipment and process Different processes, such as reflow and wave soldering, have different component layouts When reflow soldering on both sides, the layout of side A and side B also have different requirements; Selective wave soldering and traditional wave soldering also have different requirements
Basic requirements The layout design of surface mount process components is as follows:
The components on the printed circuit board shall be distributed as evenly as possible. During reflow soldering, the heat capacity of large parts is relatively large. Too high concentration can easily lead to low local temperature and lead to faulty soldering. At the same time, the uniform layout is also conducive to the balance of the center of gravity. In, components, metalized holes, and pads are not easily damaged.
The arrangement direction of components on the printed circuit board. Similar components should be arranged in the same direction as far as possible, and the characteristic direction should be consistent, so as to facilitate the placement, welding and testing of components. For example, the anode of the electrolytic capacitor, the anode of the diode, the single pin end of the triode and the first pin of the integrated circuit are arranged in the same direction as far as possible. All part numbers are printed in the same direction.
The size of the heater head of the operable SMD rework equipment shall be kept around large parts.
Temperature sensitive parts shall be kept away from heating parts. For example, 3-pole transistors, integrated circuits, electrolytic capacitors and some plastic housing components should be as far away from bridge stacks, high-power components, heat sinks and high-power resistors as possible.
The layout of parts and components that need to be adjusted or frequently replaced, such as potentiometers, adjustable inductance coils, variable capacitance microswitches, fuses, buttons, fasteners and other components, shall consider the structural requirements of the whole machine. Place it in a position that is easy to adjust and replace. If it is adjusted inside the machine, it should be placed on the printed circuit board that is easy to adjust; If the adjustment is made outside the machine, its position should be suitable for the position of the adjustment knob on the chassis panel to prevent conflicts between 3D space and 2D space. For example, the panel opening of the toggle switch and the vacant position of the switch on the printed circuit board should match.
Fixing holes shall be provided near the center of terminals, inserts, long series terminals and frequently stressed parts, and corresponding space shall be reserved around the fixing holes to prevent deformation due to thermal expansion. If the thermal expansion of long series terminals is more serious than that of printed circuit boards, it is easy to warp during wave soldering.
Some components and parts (such as transformer, electrolytic capacitor, varistor, bridge stack, radiator, etc.) requiring secondary processing due to large volume (area) tolerance and low accuracy are separated from other components. Add some allowance on the basis of setting.
For electrolytic capacitors, varistors, bridges, polyester capacitors, etc., it is recommended to add a margin of not less than 1mm; for transformers, radiators and resistors exceeding 5W (including 5W), it is recommended to add a margin of not less than 3mm
The electrolytic capacitor shall not touch the heating parts, such as high-power resistance thermistor, transformer, radiator, etc. The minimum distance between electrolytic capacitor and radiator is 10mm, and the minimum distance between other parts and radiator is 20mm.
Do not place stress sensing elements near corners, edges, or connectors, mounting holes, slots, notches, gaps, and corners of printed circuit boards. These locations are high stress areas of the printed circuit board. It is easy to lead to cracks or cracks in welding spots and components.
The layout of SMT components must meet the process requirements and spacing requirements of reflow and wave soldering. Reduce shadow effect during wave soldering.
The position of PCB positioning hole and fixing bracket shall be reserved.
When designing a large area PCB with an area greater than 500cm2, in order to prevent the PCB from bending when passing through the tin furnace, a 5~10mm wide gap should be left between the PCB without components (wiring is allowed) to prevent the PCB from bending when passing through the tin furnace.
Element arrangement direction of SMT reflow process.
1. The placement direction of components shall consider the direction of PCB entering the reflux furnace.
2. In order to heat the welding end of the chip modules at both ends and the pins on both sides of the SMD module synchronously, the tombstone, displacement and welding end caused by simultaneous heating of the welding ends on both sides of the module are reduced. For welding defects such as magnets, the long axis of the chip assemblies at both ends of the printed circuit board shall be perpendicular to the conveyor belt direction of the reflux furnace.
3. The long axis of the SMD module shall be parallel to the conveying direction of the reflux furnace, and the long axis of the chip modules at both ends shall be perpendicular to the long axis of the SMD module.
4. A good component layout design should not only consider the uniform heat capacity, but also consider the arrangement direction and order of components.
5. For large size PCB, in order to make the temperature on both sides of PCB as consistent as possible, the long side of PCB should be parallel to the direction of reflux furnace conveyor belt. Recall that when the size of the printed circuit board is larger than 200mm, the requirements are as follows:
A) The long axis of the chip assemblies at both ends is perpendicular to the long edge of the printed circuit board.
B) The long axis of the SMD assembly is parallel to the long side of the printed circuit board.
C) The printed circuit board is assembled on both sides, and the component directions on both sides are the same.
D) The arrangement direction of PCB components on the printed circuit board. Similar components should be arranged in the same direction as far as possible, and the characteristic direction should be consistent, so as to facilitate the installation, welding and testing of components. For example, the anode of the electrolytic capacitor, the anode of the diode, the single pin end of the triode and the first pin of the integrated circuit are arranged in the same direction as far as possible.
In order to prevent the interlayer short circuit PCB processing caused by contacting the printed circuit during operation, the distance between the conductive patterns on the inner and outer edges of the PCB should be greater than 1.25 mm When the outer edge of PCB has been laid with ground wire, the ground wire can occupy the edge position For the position occupied by PCB due to structural requirements, no components and printed lines can be placed The bottom pad area of SMD shall be free of through-hole/SMC to avoid heating and remelting solder in wave soldering after reflow soldering diversion.
Installation spacing of components: the minimum installation spacing of components must meet the requirements for manufacturability, testability and maintainability of SMT chip processing.
The layout of components shall be based on SMT wafer processing production equipment and process Different processes, such as reflow and wave soldering, have different component layouts When reflow soldering on both sides, the layout of side A and side B also have different requirements; Selective wave soldering and traditional wave soldering also have different requirements
Basic requirements The layout design of surface mount process components is as follows:
The components on the printed circuit board shall be distributed as evenly as possible. During reflow soldering, the heat capacity of large parts is relatively large. Too high concentration can easily lead to low local temperature and lead to faulty soldering. At the same time, the uniform layout is also conducive to the balance of the center of gravity. In, components, metalized holes, and pads are not easily damaged.
The arrangement direction of components on the printed circuit board. Similar components should be arranged in the same direction as far as possible, and the characteristic direction should be consistent, so as to facilitate the placement, welding and testing of components. For example, the anode of the electrolytic capacitor, the anode of the diode, the single pin end of the triode and the first pin of the integrated circuit are arranged in the same direction as far as possible. All part numbers are printed in the same direction.
The size of the heater head of the operable SMD rework equipment shall be kept around large parts.
Temperature sensitive parts shall be kept away from heating parts. For example, 3-pole transistors, integrated circuits, electrolytic capacitors and some plastic housing components should be as far away from bridge stacks, high-power components, heat sinks and high-power resistors as possible.
The layout of parts and components that need to be adjusted or frequently replaced, such as potentiometers, adjustable inductance coils, variable capacitance microswitches, fuses, buttons, fasteners and other components, shall consider the structural requirements of the whole machine. Place it in a position that is easy to adjust and replace. If it is adjusted inside the machine, it should be placed on the printed circuit board that is easy to adjust; If the adjustment is made outside the machine, its position should be suitable for the position of the adjustment knob on the chassis panel to prevent conflicts between 3D space and 2D space. For example, the panel opening of the toggle switch and the vacant position of the switch on the printed circuit board should match.
Fixing holes shall be provided near the center of terminals, inserts, long series terminals and frequently stressed parts, and corresponding space shall be reserved around the fixing holes to prevent deformation due to thermal expansion. If the thermal expansion of long series terminals is more serious than that of printed circuit boards, it is easy to warp during wave soldering.
Some components and parts (such as transformer, electrolytic capacitor, varistor, bridge stack, radiator, etc.) requiring secondary processing due to large volume (area) tolerance and low accuracy are separated from other components. Add some allowance on the basis of setting.
For electrolytic capacitors, varistors, bridges, polyester capacitors, etc., it is recommended to add a margin of not less than 1mm; for transformers, radiators and resistors exceeding 5W (including 5W), it is recommended to add a margin of not less than 3mm
The electrolytic capacitor shall not touch the heating parts, such as high-power resistance thermistor, transformer, radiator, etc. The minimum distance between electrolytic capacitor and radiator is 10mm, and the minimum distance between other parts and radiator is 20mm.
Do not place stress sensing elements near corners, edges, or connectors, mounting holes, slots, notches, gaps, and corners of printed circuit boards. These locations are high stress areas of the printed circuit board. It is easy to lead to cracks or cracks in welding spots and components.
The layout of SMT components must meet the process requirements and spacing requirements of reflow and wave soldering. Reduce shadow effect during wave soldering.
The position of PCB positioning hole and fixing bracket shall be reserved.
When designing a large area PCB with an area greater than 500cm2, in order to prevent the PCB from bending when passing through the tin furnace, a 5~10mm wide gap should be left between the PCB without components (wiring is allowed) to prevent the PCB from bending when passing through the tin furnace.
Element arrangement direction of SMT reflow process.
1. The placement direction of components shall consider the direction of PCB entering the reflux furnace.
2. In order to heat the welding end of the chip modules at both ends and the pins on both sides of the SMD module synchronously, the tombstone, displacement and welding end caused by simultaneous heating of the welding ends on both sides of the module are reduced. For welding defects such as magnets, the long axis of the chip assemblies at both ends of the printed circuit board shall be perpendicular to the conveyor belt direction of the reflux furnace.
3. The long axis of the SMD module shall be parallel to the conveying direction of the reflux furnace, and the long axis of the chip modules at both ends shall be perpendicular to the long axis of the SMD module.
4. A good component layout design should not only consider the uniform heat capacity, but also consider the arrangement direction and order of components.
5. For large size PCB, in order to make the temperature on both sides of PCB as consistent as possible, the long side of PCB should be parallel to the direction of reflux furnace conveyor belt. Recall that when the size of the printed circuit board is larger than 200mm, the requirements are as follows:
A) The long axis of the chip assemblies at both ends is perpendicular to the long edge of the printed circuit board.
B) The long axis of the SMD assembly is parallel to the long side of the printed circuit board.
C) The printed circuit board is assembled on both sides, and the component directions on both sides are the same.
D) The arrangement direction of PCB components on the printed circuit board. Similar components should be arranged in the same direction as far as possible, and the characteristic direction should be consistent, so as to facilitate the installation, welding and testing of components. For example, the anode of the electrolytic capacitor, the anode of the diode, the single pin end of the triode and the first pin of the integrated circuit are arranged in the same direction as far as possible.
In order to prevent the interlayer short circuit PCB processing caused by contacting the printed circuit during operation, the distance between the conductive patterns on the inner and outer edges of the PCB should be greater than 1.25 mm When the outer edge of PCB has been laid with ground wire, the ground wire can occupy the edge position For the position occupied by PCB due to structural requirements, no components and printed lines can be placed The bottom pad area of SMD shall be free of through-hole/SMC to avoid heating and remelting solder in wave soldering after reflow soldering diversion.
Installation spacing of components: the minimum installation spacing of components must meet the requirements for manufacturability, testability and maintainability of SMT chip processing.
Just upload Gerber files, BOM files and design files, and the KINGFORD team will provide a complete quotation within 24h.