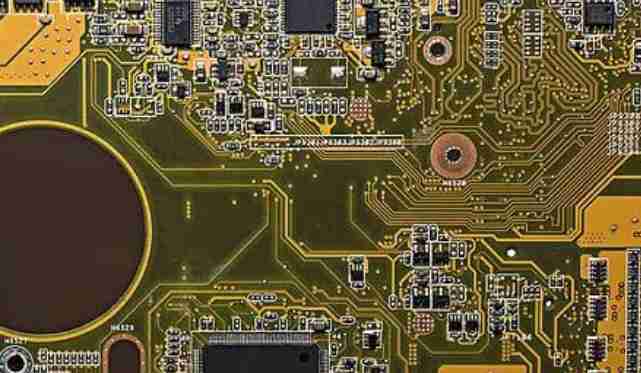
Another method is to systematically bake all the parts left after production using drag trays and rolls. This is a simpler admin program, but it can create more problems than it actually defends. It is important to note that the default conditions for barium drying have been significantly increased in the latest IPC/JEDEC standard. For parts packed in high temperature trays, the cycle is now 125°C 48 hours. The components on the roll and low temperature strip must be baked at 40°C for 68 days. At most companies, this is simply impossible. The standard states that unless otherwise indicated, the baking cycle is permissible on the finished component. If more than one cup drying cycle is required, the supplier should be consulted.
Manual recording time
In many companies, the MSD program requires the production operator to manually record the date and time the part was originally taken out of its protective drying bag. Because most MSDS are packaged in a JEDEC/EIAJ tray or reel, exposure time records (for those on reel) can be included in a label. In the case of a pallet, there is no way to attach the processing data directly to the container. Because of these limitations, it is difficult to maintain the connection between the components and their respective recording tables, as the tray and reel are removed from the mounter and drying chamber.
In addition to the record sheet actual
Outside of the physical format, the dynamically changing data it contains creates further difficulties. The information must include the part number and sensitivity level, as this data is lost after the bag is opened and thrown away. In order to track exposure time, the log sheet must include at least one column to record the date and time when the bag was first opened. In order for the procedure to count the time spent in dry storage, the record sheet must also include the date and time (possibly multiple times) when the material entered and was removed from the drying chamber or bag.
The biggest difficulty with this type of manual recording is that date and time-based calculations are not simple algebraic operations. It takes a lot of time and effort, even for well-trained people, and it invites human error. The time spent on this also has a direct impact on the overhead time and machine/line utilization.
Inspection of feeder and mounter
A time logging program during material movement is a good start; However, it hardly provides any visible part status when mounted on the mounter. Why is this important? It may be that individual components will eventually exceed the maximum exposure time because this is where they spend the most time.
Part of the measurement of drying control can be achieved by regular inspection. The frequency of inspection is largely determined by the sensitivity level and the number of product conversions and related feeder Settings. In fact, it means that the production operator must make additional date and time calculations based on the previous records and finally remove the component from the mounter before it expires.
Due to the lack of visibility, MSDS mounted on machine and feeder mounts may be exposed for a longer period of time. Great care should be taken with lines with fixed feeder Settings and unused trays and coils that are not removed from the machine.
In addition to these concerns, there are other difficulties associated with the process in question. This includes baking, resealing in dry bags, re-labeling, repair and rework, equipment programming, reloading tape, double-sided reflux, indoor condition degradation, etc.
conclusion
There are a number of large barriers preventing assembly manufacturers from properly controlling damage to MSDS. In many cases, there are sufficient written procedures, but they immediately become artificially unfollowed. This creates an unacceptable number of defects. PCB assembly operations should re-evaluate their MSD work procedures against the latest IPC/JEDEC standard. Although the control of moisture hazards is just as important as static damage, it does not receive the same attention. New systems and methods are required to provide viable and reliable solutions to such problems in production environments.