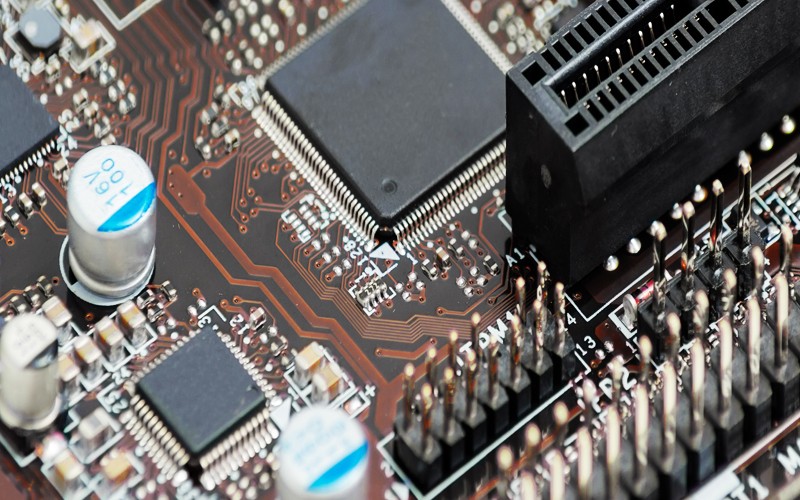
Why is flux so important for PCBA circuit board welding?
Flux: a chemICal substance that can help and promote the welding process in the welding process, and has a protective effect and prevents oxidation reaction. Flux can be divided into solid, liquid and gas. It mainly includes "auxiliary heat conduction", "removing oxides", "reducing the surface tension of the welded material", "removing the oil stain on the surface of the welded material, increasing the welding area", and "preventing reoxidation". The two key roles in these aspects are "removing oxides" and "reducing the surface tension of the welded material".
Flux is usually a mixture of rosin as the main component, which is an auxiliary material to ensure the smooth welding process. Welding is the main process in electronic assembly. Flux is the auxiliary material used in welding. The main function of flux is to remove the oxides on the surface of solder and the base metal to make the metal surface reach the necessary cleanliness. It prevents the surface from re oxidation during welding, reduces the surface tension of solder, and improves the welding performance. The performance of flux directly affects the quality of electronic products.
Flux is an important auxiliary material in PCBA circuit board welding. The quality of flux will directly affect the quality of PCBA circuit board welding. Let me analyze why it is so important.
1. Principle of flux welding
The reason why the flux can bear the welding effect is that the metal atoms are close to each other, resulting in mutual diffusion, dissolution, infiltration and other effects. In addition to the activation performance of removing oxides and pollutants, the flux should also meet the requirements of non corrosion, insulation, moisture resistance, stability, harmlessness, purity, etc. Generally speaking, its main components include active agent, film-forming material, additive, solvent, etc.
2. Remove oxides on the surface of the welded metal
In the normal air environment, there are always some oxides on the metal surface of the pad. These oxides will affect the wetting of the solder during welding, thus affecting the welding process and welding results. Therefore, the flux needs to be able to restore the oxides, and the welding of PCBA processing can be carried out normally.
3. Prevention of secondary oxidation
During the welding process of PCBA processing, heating is required. However, during the heating process, the metal surface will appear rapid oxidation due to the increase of temperature. At this time, flux is required to play a role in preventing secondary oxidation.
4. Reduce the tension of molten solder
Due to the physical form, the surface of the molten solder will have a certain tension, which will lead to the speed of the solder flowing to the surface to be welded, thus affecting the normal wetting during the welding process. At this time, the role of the flux is to reduce the surface tension of the liquid solder, so that the wettability can be significantly improved.
The above is why flux is so important for PCBA circuit board welding. After using flux, PCB boards need to clean residues on the surface in time. How to select surface cleaning solvent